自1974年以来,Specialized的目标一直是:以创新和激励来并提高骑手的生活。借助Carbon的3D打印平台,Specialized发现了一种新的方法来解决车手普遍面临的挑战,其速度是正常开发过程的两倍。
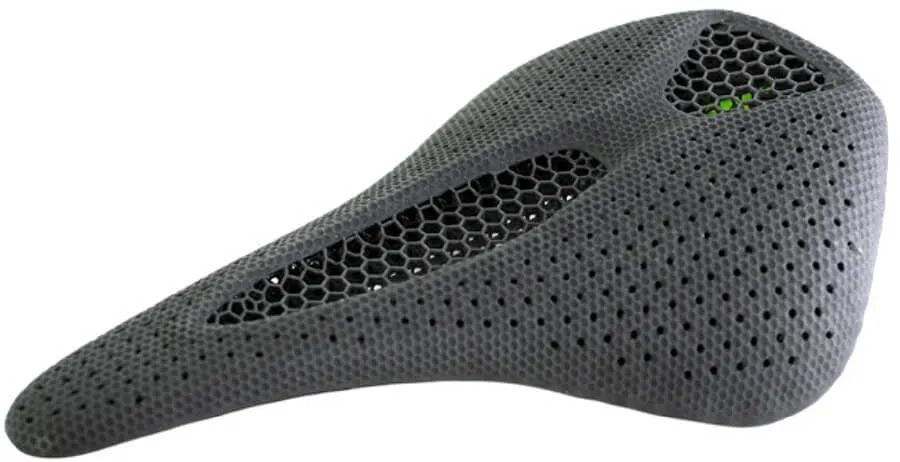
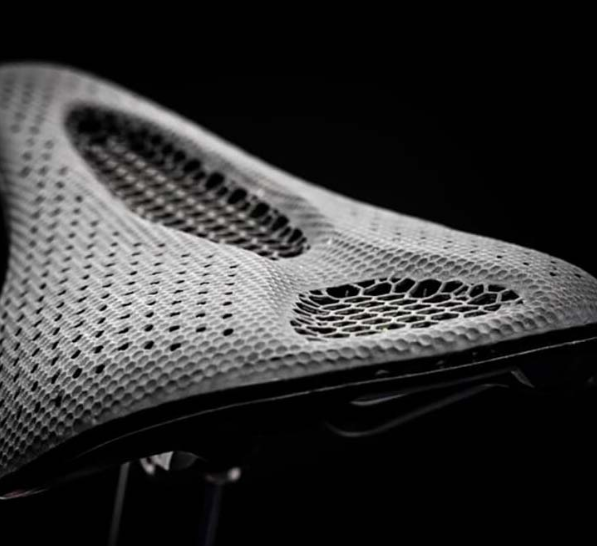
挑战
对于各个级别的骑手来说,骑行体验中最重要的一项便是自行车鞍座。舒适就意味着发挥的淋漓尽致,因为不舒适经常被视为放弃这项运动的原因。二十多年来,Specialized努力解决这一问题,使用不同类型泡沫最终达到了传统制造方法的实施极限。
Specialized过去的自行车鞍座是通过组合三种类型的泡沫,为不同的功能区提供不同的硬度;但是,对于Specialized来说,没有实际的方法来添加更多的区域。
Specialized需要开发一种能够最大限度地发挥性能自行车鞍座,同时提供舒适性和稳定性。然而,缺少两个重要因素,一种允许马鞍密度无限变化的材料,以及一种建立理想舒适区的生产工艺。
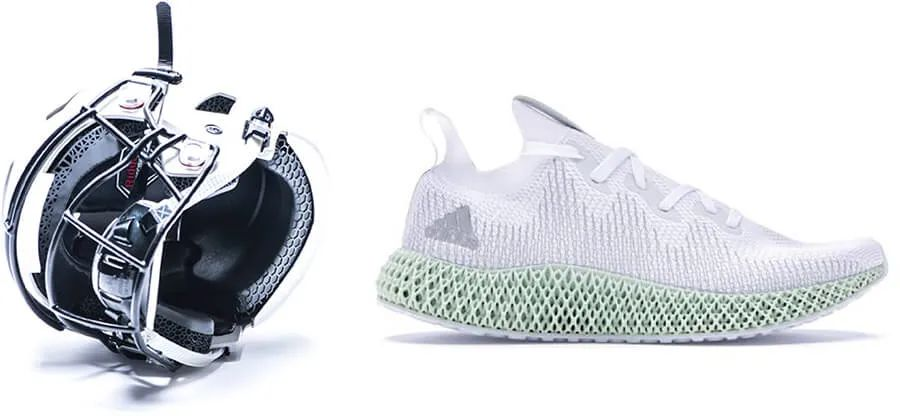
量化和实现舒适度
设计优质而高性能的自行车座垫需要回归到基本原理。哪些设计元素会提高骑车人的舒适度?Specialized如何使用增材制造来构建实验以更好地了解产品与市场的契合度?
冲击吸收或能量回弹?
Carbon EPU树脂的弹性体晶格将撕裂强度,能量返回和伸长率结合在一起,非常适合此应用,使其非常适合缓冲,冲击吸收和避震。
如果有选择的话,车手会喜欢更小的冲击力还是更大的能量回报?为了回答这个问题,Specialized使用Carbon技术测试了同样的鞍座设计,这种设计采用了两种不同的材料:一种用于吸收冲击,另一种用于能量回弹。
虽然从直觉上看,增加冲击吸收将产生更平稳的乘坐,但实际上,当座椅吸收冲击时,它会慢慢压缩,最终降低舒适性。骑手们显然更喜欢能量回弹来保持他们的位置。
更舒适还是更可控?
当你可以两者兼得时,为什么还需要选择?专业理论认为,虽然创造容易压缩的区域可以提高舒适性,但骑手仍然需要一定的支撑和压力来帮助稳定和血液流动。基于该理论的第一个设计在骑手的尾骨部位使用了一个大而柔软的空槽。测试表明,类似凝胶鞍座的均匀的柔软度会导致不稳定性,并降低骑手的控制力。这个问题通过压力梯度得到了解决,将尾骨位于柔软的中心,并逐渐地增加在鞍座的中部左右两块坐骨区域的硬度。这个设计的结果是一个完美的组合:一个自行车鞍座,它能最佳地分配压力以增加舒适度,同时给骑手以他们需要的可控性来达到最佳的表现(图3)。
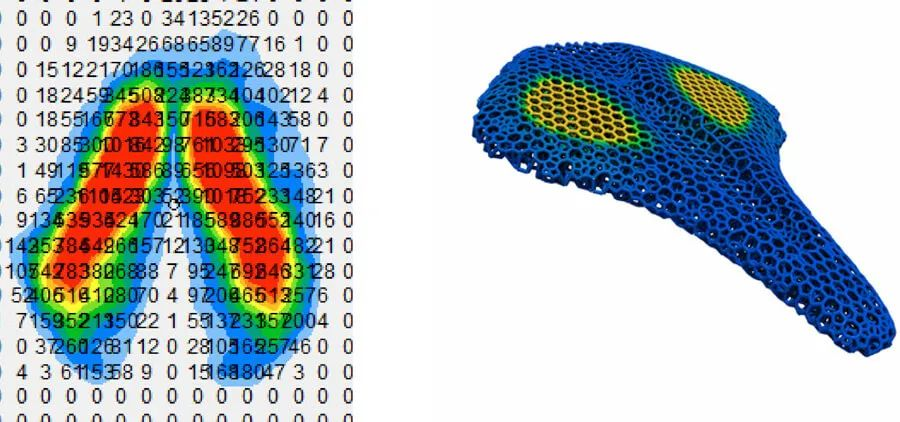
端到端生产解决方案
Specialized最终开发出了这种由弹性晶格制成的自行车鞍座,它完全符合骑手对较低峰值压力的要求,且具备了更为平缓的压力分布,继而采用Carbon平台完成了其规模化生产。同时,Carbon也开发了一种新技术,使用准分子光源来定制设计微观表面,使鞍座以高端的哑光表面展现了其完美的抓力。这款产品的成功标志着新技术首次应用于商业化的3D打印领域。
骑手舒适度的突破
借助Carbon平台,Specialized最终能够将生产时间从24个月减少至10个月:创下开发新自行车鞍座的最短记录。
从文档到现实
第一步:探索技术可行性
持续时间:1个月
迭代:10个设计周期
成功标准:
- 材料:Carbon EPU系列
- 印刷样品:第一个鞍座
ALPHA阶段:概念证明
持续时间:6个月
迭代:40个设计周期
成功标准:
- 环境:通过核心材料要求
- 材质锁:EPU 41黑色
- 设计:核心晶格配置
- 表现:绝大多数车手提供了正面反馈
- 压力图:较低的峰值压力+较平滑的压力梯度
- 设计装配工装+启动
BETA阶段:设计验证
持续时间:5个月
迭代:30个设计周期
成功标准:
- 可扩展的端到端制造流程:
- 生产解决方案:L1打印机
- 后处理:清洁(无溶剂)+ 烘烤
- 最终的优质工业设计:
- 质地和表面处理:准分子光源的磨砂处理
- 开发并交付了先进的制造工艺
试产阶段:生产开始
时间:1个月
迭代:经过验证的初步设计并实施了改进的组装流程
成功标准:
- 确定解决,实施和集成到生产线中的核心问题
- 继续获得绝大多数车手的好评